O balanceamento de ferramentas de corte é um processo essencial para garantir o funcionamento adequado e a durabilidade de componentes rotativos em máquinas industriais, como fresadoras CNC, centros de usinagem e mandriladoras. Quando um componente rotativo não está devidamente balanceado, forças desequilibradas geram vibrações que comprometem o desempenho, a segurança e a vida útil do equipamento. Esse desbalanceamento ocorre devido à distribuição irregular de massa ao redor do eixo de rotação, fazendo com que o centro de massa da peça não coincida com o eixo de rotação.
A importância do balanceamento de ferramentas de corte no processo de usinagem
O balanceamento do conjunto ferramenta de corte e cone é essencial tanto para máquinas de alta rotação, como centros de usinagem high speed, quanto para equipamentos com rotação mais baixa, como fresadoras CNC que operam entre 6.000 e 8.000 rpm. Apesar disso, essa não é uma prática comum e possui diversas consequências no processo produtivo.
Dentre os problemas causados por negligenciar esse processo estão o desgaste acelerado das ferramentas de corte, a necessidade de manutenção prematura do spindle da máquina e um acabamento superficial comprometido. Este conjunto de fatores eleva os custos, reduz a repetibilidade e compromete a qualidade da peça final.
Atualmente, os principais fabricantes de ferramentas e cones realizam o balanceamento de seus produtos por meio de simulações em software durante o projeto (by design). Entretanto, muitos desses produtos não passam por um balanceamento físico. Portanto, o balanceamento de ferramentas de corte e cones é fundamental para assegurar qualidade, repetibilidade e gestão de custos na produção.
Além disso, mesmo que todas as ferramentas de corte e cones fossem balanceados individualmente, o conjunto ainda apresentaria desbalanceamento após a montagem, de forma semelhante ao que ocorre com o pneu de um carro montado em uma roda. Sendo assim, é importante que o processo seja realizado com o conjunto acoplado.
Porém se engana quem acredita que o balanceamento deve ser feito apenas uma vez, pois o desgaste natural da ferramenta durante a usinagem altera a distribuição de massa do conjunto. A fim de manter o desbalanceamento residual dentro dos limites aceitáveis deve ser realizada a correção periódica do balanceamento. Normalmente, esse processo segue a norma ISO 1940-1, buscando um nível de qualidade elevado, como G 2,5.
Como acontece o balanceamento de ferramentas de corte
O processo de balanceamento de ferramentas de corte e cones é relativamente simples. Equipamentos especializados, como a máquina balanceadora Haimer apresentada no Gif 1, realizam algumas rotações e indicam ao operador onde e quanto de massa deve ser adicionada ou removida ao conjunto para corrigir o desbalanceamento. Após a correção, o operador deve realizar uma nova avaliação na máquina balanceadora para verificar se o balanceamento foi bem-sucedido. Em situações de desequilíbrio extremo, pode ser necessário remover material do cone por meio de usinagem, especialmente quando o volume de massa desequilibrada é elevado.
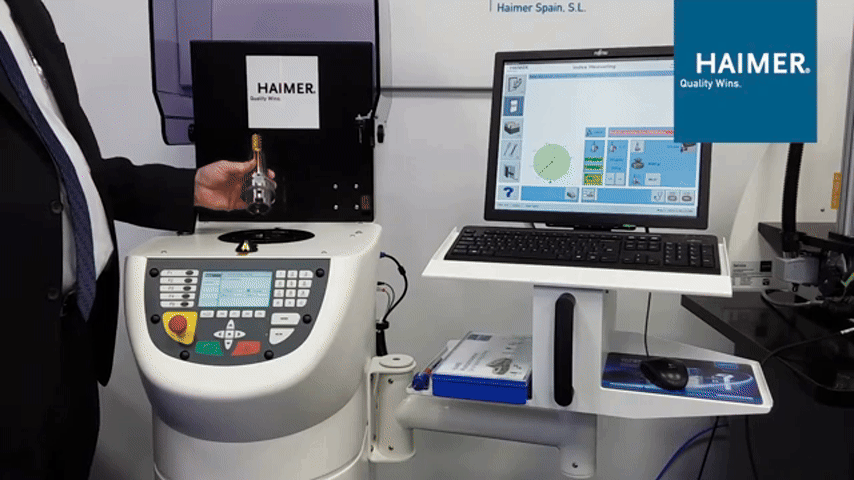
Gif 1 – Máquina balanceadora Haimer. Fonte: https://www.youtube.com/@HaimerGermany
Como o balanceamento pode melhorar a produção: Estudo de caso no setor automotivo
Durante o processo comercial, a equipe da Haimer identificou um problema de desbalanceamento de ferramentas de corte no processo de usinagem em um cliente do setor automotivo. A equipe de engenharia de aplicação realizou um estudo detalhado e apresentou um relatório técnico ao cliente, evidenciando os ganhos potenciais com a implementação de um balanceamento adequado das ferramentas. Curiosamente, o cliente enfrentava os problemas há algum tempo, sem perceber que o desbalanceamento era a causa raiz e que a implementação do balanceamento poderia impactar positivamente o seu processo.
Principais problemas antes do balanceamento
O problema estava em uma broca de 6 mm de diâmetro, com duas arestas de corte, operando a uma rotação de 5.300 rpm. Essa condição desfavorável gerava diversos efeitos negativos no processo. Sendo assim, o cliente relatou os seguintes problemas em seu processo de usinagem:
- Vida útil da ferramenta não constante: a ferramenta apresentava desgaste diferente para diferentes unidades do mesmo modelo;
- Frequentes quebras de ferramenta: resultando em custos elevados com reposição e reparos, além de maior tempo de máquina parada, reduzindo a produtividade;
- Paradas de máquina não programadas: impactando diretamente na produtividade;
- Número excessivo de set-ups: prejudicando o ritmo de produção;
- Desgaste irregular ao longo da geometria da ferramenta: comprometendo a precisão do processo;
- Dificuldades na reafiação: o desgaste irregular dificultava a reafiação da ferramenta, gerando perdas significativas.
Esses problemas não apenas aumentavam o consumo de ferramentas, elevando os custos operacionais, como também reduziam a capacidade produtiva devido às frequentes interrupções e necessidade de ajustes.
Como o balanceamento resolveu os problemas detectados
A Haimer identificou duas oportunidades principais para o cliente: reduzir o consumo de ferramentas e aumentar a produtividade. Embora o ganho com a redução do desgaste do spindle também fosse relevante, sua mensuração exigiria um período prolongado de testes, razão pela qual esse fator foi desconsiderado na análise.
O cliente enviou um conjunto cone-ferramenta com o problema para a equipe de engenharia de aplicação da Haimer, localizada em Campinas/SP. Os engenheiros posicionaram o conjunto em uma máquina balanceadora e identificaram um desbalanceamento residual de 23,5 gmm, correspondente a uma classe de desbalanceamento de G13.1. Esse valor indicava que a ferramenta estava severamente desbalanceada, afetando diretamente o desempenho e a durabilidade do processo de usinagem. A Figura 1 apresenta o desbalanceamento inicial detectado pela máquina balanceadora Haimer.spondente a uma classe de desbalanceamento de G13.1. Esse valor indicava que a ferramenta estava severamente desbalanceada, afetando diretamente o desempenho e a durabilidade do processo de usinagem. A Figura 1 apresenta o desbalanceamento inicial detectado pela máquina balanceadora Haimer.
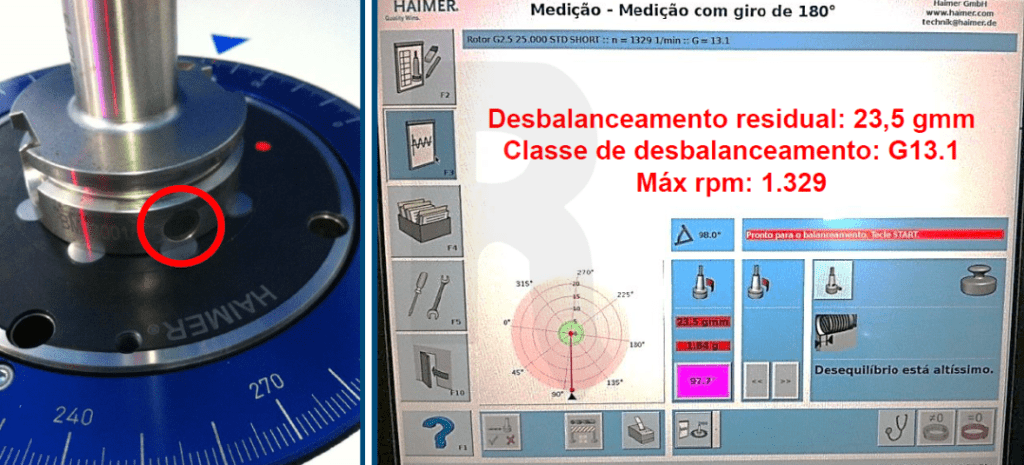
Figura 1 – Desbalanceamento inicial da ferramenta do cliente na balanceadora.
Após o balanceamento do conjunto, o desbalanceamento residual foi reduzido para 5,0 gmm, equivalente a uma classe de desbalanceamento de G1.0. Essa classe é considerada excelente para ferramentas de alta precisão, evidenciando a eficácia do processo de balanceamento. A Figura 2 apresenta o resultado após o balanceamento.
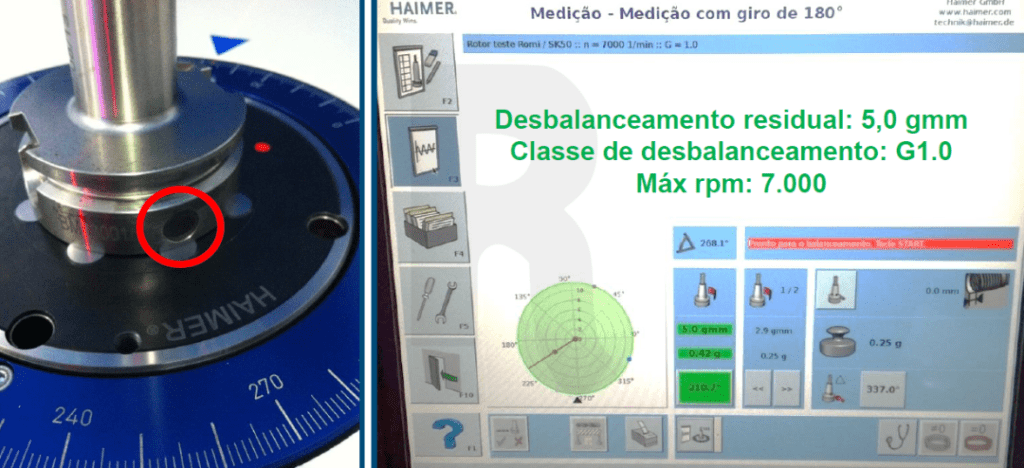
Figura 2 – Desbalanceamento da ferramenta do cliente após o balanceamento.
Os dados coletados antes e depois do balanceamento confirmaram uma melhora significativa no processo produtivo. A quantidade de peças produzidas antes de ser necessário enviar a ferramenta para afiação aumentou de 600 para 1.200 unidades, dobrando a capacidade produtiva da ferramenta por afiação. Além disso, a produção média por hora teve um leve aumento, passando de 11,32 para 11,34 peças/h. A Tabela 1 resume os principais resultados obtidos.
PARÂMETROS ANALISADOS | DESBALANCEADO | BALANCEADO |
---|---|---|
Classe de desbalanceamento | G 13,1 | G 1,0 |
Número de peças produzidas a cada afiação (média) | 600 | 1200 |
No. de quebras (média/mês) | 14 | 0 |
Paradas de máquina | Diversas | Programadas |
Número de Set-Up | Diversos | Programados |
Desgaste constante | Não | Sim |
Quantidade de reafições | 3 | 6 |
Processo estável | x | OK |
Tabela 1 – Comparação dos dados antes e depois do balanceamento.
Outro benefício relevante foi a uniformização do desgaste da ferramenta. Antes do balanceamento, o desgaste ocorria de maneira irregular, comprometendo a reafiação. Após o balanceamento, o desgaste se tornou homogêneo, permitindo o dobro de reafiações e, consequentemente, reduzindo pela metade a necessidade de troca de ferramentas. A Figura 3 apresenta o desgaste da ferramenta antes e depois do balanceamento.
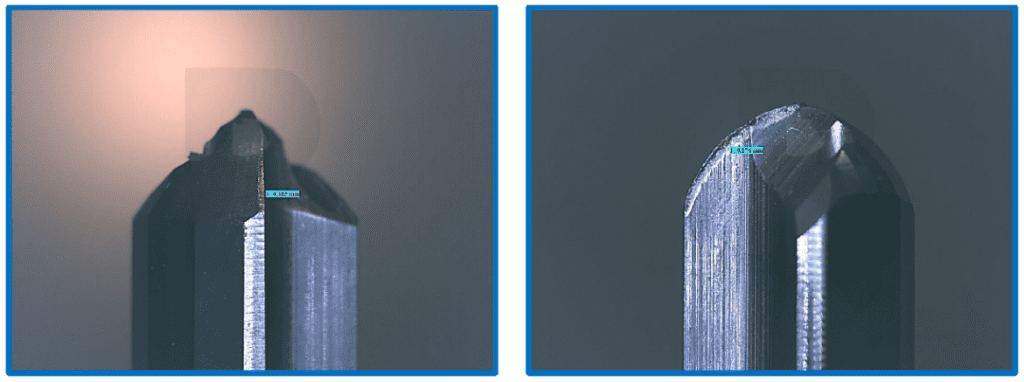
Figura 3 – Desgaste da ferramenta antes (esquerda) e depois (direita) do balanceamento.
Conclusão
Investir em um processo de balanceamento de ferramentas de corte adequado não apenas prolonga a vida útil dos componentes da máquina e reduz custos com manutenção, mas também proporciona um trabalho mais produtivo. Portanto, o balanceamento deve ser tratado como uma prática padrão em qualquer operação de usinagem, independentemente da rotação.
No estudo de caso apresentado, o balanceamento das ferramentas realizado pela Haimer proporcionou ganhos significativos em termos de durabilidade das ferramentas e eficiência produtiva. A redução no desbalanceamento resultou na duplicação da quantidade de reafiações, reduziu o número de quebras e as paradas de máquinas.
A análise detalhada e o suporte técnico especializado da Haimer permitiram identificar e corrigir um problema crítico que o cliente desconhecia, transformando um gargalo produtivo em uma oportunidade de melhoria contínua. O sucesso desse projeto reforça a importância do balanceamento em processos de usinagem.
A Róiz Máquinas, representante da Haimer em Minas Gerais, está à disposição para demonstrações e testes práticos, possibilitando que nossos clientes comprovem os ganhos no processo. Fale com nossos especialistas e descubra como otimizar a produção da sua empresa.
Referências
- Catálogo Haimer – TOOL DYNAMIC;
- Acervo Haimer Brasil;
- Norma ISO 16084 e ISO 1940-1.