A escolha do cone porta-ferramenta, também conhecido como mandril de usinagem ou interface máquina-ferramenta, desempenha um papel crucial na usinagem de alta precisão. Ela impacta diretamente a rigidez do sistema, a transmissão de torque, a estabilidade térmica e a vida útil das ferramentas.
Em um mercado cada vez mais exigente, a escolha correta desse sistema pode ser o diferencial entre uma produção eficiente e uma série de falhas operacionais. Dentre as interfaces mais utilizadas, os sistemas BT e HSK se destacam por suas características únicas e aplicabilidades distintas. No entanto, ainda existem outras tecnologias como o CAT e SK que também são descritos nesse post.
Comparativo entre os sistemas BT, CAT, SK e HSK presentes nos cones porta-ferramenta
O sistema de fixação BT
O cone com sistema de fixação BT, também conhecido como Big Taper, é amplamente utilizado em centros de usinagem no Brasil, sendo especialmente valorizado por sua confiabilidade, versatilidade e excelente relação custo-benefício. Desenvolvido originalmente no Japão, o sistema BT se caracteriza por seu design simétrico e por utilizar um ângulo cônico de 7/24, o mesmo presente nos sistemas CAT e SK. Isso significa que, a cada 24 unidades de comprimento, há um afunilamento de 7 unidades, o que proporciona uma fixação estável e relativamente precisa.
A linha BT é composta por diferentes modelos de cones porta-ferramenta, entre os quais se destacam o BT30, o BT40 e o BT50. Cada um é adequado para diferentes tipos de aplicações, variando conforme a robustez exigida, a potência da máquina e o tipo de material a ser usinado. O número 30 refere-se ao diâmetro nominal do cone (30 mm), sendo essa a versão mais leve e compacta da família.
O modelo BT30 é indicado para centros de usinagem menores, com foco em operações leves, de alta rotação e que exijam trocas de ferramentas mais rápidas. Por apresentar menor massa, exerce menos esforço sobre o spindle e é especialmente vantajoso em aplicações que demandam agilidade e precisão sem grandes esforços de corte. Apesar de sua menor rigidez em comparação com modelos maiores, ele tem sido amplamente adotado em linhas de produção onde o tempo de ciclo e a eficiência operacional são prioridades.
Já o modelo BT40 é o mais popular da linha e é amplamente empregado em centros de usinagem de médio porte, como os utilizados em máquinas das marcas Romi e Travis. O BT40 é uma solução bastante versátil e adequada para operações de média complexidade, sendo ideal para aplicações em que o equilíbrio entre desempenho e custo operacional é fundamental. Uma de suas principais vantagens é a massa reduzida em comparação ao BT50, possibilitando alcançar rotações mais elevadas. Além disso, seu custo mais acessível o torna uma escolha frequente para empresas que buscam produtividade com investimentos otimizados.
Por outro lado, o cone BT50 é o mais robusto da linha, com diâmetro nominal de 50 mm. Esse modelo foi desenvolvido para suportar forças de corte mais intensas e atender às exigências de centros de usinagem maiores e mais potentes. Devido à sua estrutura reforçada, esse tipo de cone é frequentemente utilizado em processos pesados, especialmente na usinagem de materiais de alta dureza ou difícil usinagem. Sua construção oferece maior rigidez e estabilidade, permitindo uma fixação mais resistente a forças radiais e axiais. A área de contato ampliada entre o cone e o spindle contribui para a redução de vibrações e deflexões.
Apesar das vantagens, os cones da linha BT apresentam algumas limitações, principalmente relacionadas à ausência de apoio de face no sistema de fixação. Esse fator reduz a rigidez geral do conjunto, o que pode ser problemático em operações de alta rotação ou que exijam elevada precisão dimensional. A fixação puramente cônica pode gerar pequenas folgas, comprometendo a estabilidade da ferramenta e afetando negativamente a qualidade do acabamento da peça.
Além disso, a ausência de contato frontal também torna a troca de ferramentas ligeiramente mais lenta, o que pode impactar a produtividade em operações seriadas. Em resumo, a escolha entre os diferentes modelos de cones BT deve ser feita com base nas necessidades específicas de cada aplicação. A Figura 1 apresenta um exemplo de cone BT fabricado pela Haimer, empresa parceira da Róiz Máquinas e reconhecida internacionalmente pela excelência na produção de ferramentas e sistemas de fixação de alta precisão.
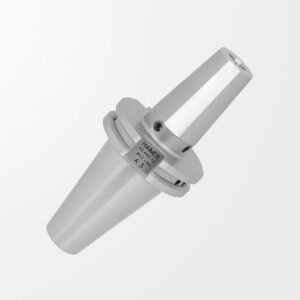
O sistema de fixação CAT
O sistema CAT, cujo nome é derivado da empresa norte-americana Caterpillar, foi desenvolvido por volta da década de 1950 nos Estados Unidos. Desde então, passou a ser amplamente utilizado em centros de usinagem americanos.
Uma distinção importante está na rosca de tração, que no sistema CAT é posicionada em apenas um dos lados do cone porta-ferramenta, tornando sua geometria assimétrica. Essa assimetria, embora não afete diretamente a rigidez, pode causar desequilíbrios em altas rotações, tornando o sistema menos adequado para aplicações de alta velocidade, onde o balanceamento dinâmico é essencial para a precisão e estabilidade do processo. Devido a essa limitação, os cones CAT não são tão comuns em aplicações modernas com exigência de alta rotação, sendo mais utilizados em processos robustos e de menor velocidade. Saiba mais sobre o balanceamento de ferramentas de corte.
Apesar dessa desvantagem em relação à rotação, os cones porta-ferramenta CAT oferecem alta rigidez estrutural, sendo bastante eficazes em operações de usinagem pesada, que exigem estabilidade e resistência a grandes forças de corte. Essa característica faz com que o sistema ainda seja encontrado em centros de usinagem mais antigos ou em linhas de produção onde a velocidade não é o principal fator de desempenho, mas sim a confiabilidade e a durabilidade do conjunto mecânico.
Outro ponto relevante é que o sistema CAT possui ampla compatibilidade com diversos modelos de máquinas nos Estados Unidos, o que contribuiu para sua ampla adoção na indústria norte-americana. No entanto, em mercados como o brasileiro, seu uso é mais restrito, especialmente diante da popularidade e ampla disponibilidade dos sistemas BT e HSK, que oferecem maior versatilidade, especialmente em operações de alta velocidade. No entanto, ao contrário dos cones BT, que são simétricos e podem ser usados em ambas as direções de rotação, o CAT é projetado principalmente para operar em rotação horária, devido à sua configuração assimétrica.
O sistema de fixação SK
Popular na Europa, o cone com fixação tipo SK, ou Steilkegel (cone íngreme, em alemão), foi desenvolvido na Alemanha. Sua aplicação é bastante comum em máquinas-ferramenta de alta precisão, como os modelos produzidos pela DMG MORI, entre outros fabricantes do continente europeu. Trata-se de um cone com geometria simétrica e ângulo de afunilamento 7/24, o mesmo utilizado nos sistemas BT e CAT, o que garante uma fixação cônica segura e eficiente.
Diferentemente do sistema CAT, o cone SK é simétrico e apresenta furo de tração em ambos os lados, similar ao cone BT. Essa simetria é especialmente vantajosa em operações de alta rotação, pois permite um melhor balanceamento dinâmico, reduzindo vibrações e contribuindo para uma usinagem mais precisa. No entanto, ao contrário do sistema BT, o SK utiliza rosca métrica para fixação do tirante, o que pode gerar incompatibilidades com centros de usinagem projetados para sistemas com rosca em polegadas.
Entre as principais características dos cones SK, destaca-se a sua excelente rigidez mecânica, que proporciona maior estabilidade em processos de corte mais exigentes. Isso faz com que o sistema seja bastante adequado para aplicações que exigem elevada precisão dimensional, como a fabricação de moldes, matrizes e peças técnicas com tolerâncias estreitas. Ainda assim, é importante observar que a eficiência do sistema está diretamente relacionada ao estado de conservação da interface cone/mandril, bem como à qualidade da montagem.
Além disso, os cones SK são reconhecidos por sua durabilidade e precisão repetitiva, características essenciais para garantir estabilidade dimensional em séries produtivas. Como o sistema foi amplamente adotado por fabricantes europeus, ainda hoje é encontrado em grande número de centros de usinagem de origem alemã, suíça e italiana, especialmente em máquinas da geração anterior à popularização do sistema HSK.
Contudo, assim como ocorre com os sistemas BT e CAT, o cone SK possui limitações quando comparado a tecnologias mais modernas, como o próprio HSK. A ausência de apoio de face reduz a rigidez total da fixação em operações com grandes esforços radiais ou axiais. Essa limitação pode resultar em pequenas deflexões durante o processo, afetando negativamente o acabamento da peça e a vida útil da ferramenta.
O sistema de fixação HSK
O cone porta-ferramenta de fixação HSK (Hohlschaftkegel), ou “cone de haste oca” em tradução literal do alemão, representa uma das mais avançadas tecnologias de fixação disponíveis atualmente para centros de usinagem de alto desempenho. Desenvolvido na Alemanha para atender às crescentes demandas por precisão, estabilidade térmica e alta rotação, o HSK se diferencia profundamente dos sistemas tradicionais como BT, CAT e SK.
Uma das características mais marcantes do cone HSK é a sua geometria cônica com proporção 1/10, ou seja, para cada 10 unidades de comprimento, há uma unidade de afunilamento, conferindo-lhe um perfil mais “curto e largo” em comparação aos sistemas convencionais com ângulo 7/24. Esse formato, somado ao design oco, permite que a fixação ocorra simultaneamente no cone e na face do porta-ferramenta, proporcionando maior rigidez, precisão e estabilidade mesmo em condições severas de corte.
Ao contrário dos cones sólidos, o HSK foi projetado levando em consideração os efeitos da expansão térmica em rotações elevadas. Em alta rotação, os fusos tendem a sofrer deformações elásticas, fenômeno conhecido como “efeito boca de sino”. Enquanto nos cones tradicionais isso pode causar perda de contato e redução da precisão, no sistema HSK o cone oco se deforma junto ao fuso, mantendo contato constante e firme ao longo de toda a superfície de acoplamento. É esse comportamento que torna o sistema ideal para aplicações com velocidades acima de 20.000 rpm, podendo superar os 50.000 rpm.
O cone HSK foi padronizado por normas DIN e segmentado em diversas variantes, de HSK-A a HSK-F, cada uma desenvolvida para atender a diferentes tipos de aplicação. As versões mais utilizadas no setor industrial são:
- HSK-A: é a versão mais comum e versátil. Possui ranhuras assimétricas na extremidade do cone, permitindo orientação única durante o acoplamento. Recomendado para aplicações de média a alta rotação (até 45.000 rpm) que também exigem torque elevado. Seu design facilita a transmissão de força e proporciona excelente rigidez. A Figura 2 mostra um exemplo de cone HSK-A da Haimer;
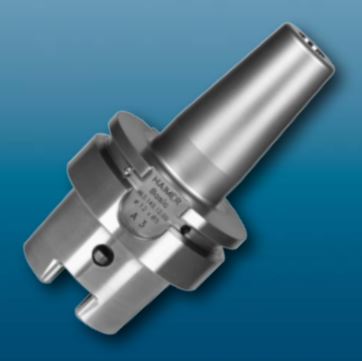
- HSK-E: destinado a aplicações com altíssimas rotações e altíssima precisão, esse modelo é bastante utilizado em processos automatizados e máquinas de alto desempenho. Elimina elementos como chavetas e ranhuras que poderiam gerar desbalanceamento, otimizando o comportamento dinâmico do conjunto. A Figura 3 mostra um exemplo de cone HSK-E da Haimer;
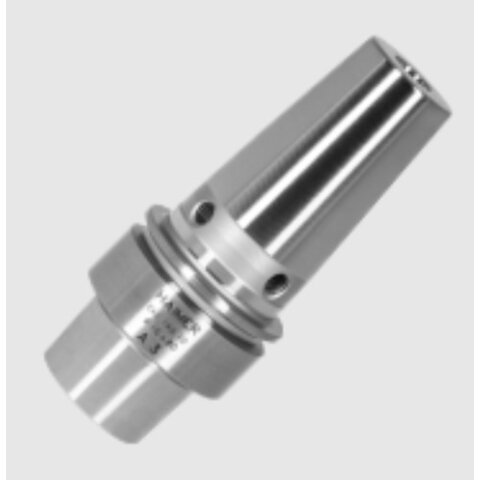
- HSK-F: Similar ao HSK-E, porém, com dimensões externas mais compactas, o que possibilita um flange maior e maior área de contato com o fuso. Sua principal vantagem está na estabilidade durante operações de altíssima rotação com baixo torque.
A principal vantagem do sistema HSK frente aos sistemas BT, CAT e SK está na fixação dupla, por cone e face, o que reduz a vibração, melhora o acabamento superficial, prolonga a vida útil da ferramenta e assegura maior repetibilidade dimensional. Soma-se a isso a possibilidade de trocas rápidas de ferramenta (quick change), fator essencial em linhas de produção automatizadas ou células robotizadas.
Entretanto, como toda tecnologia avançada, o sistema HSK apresenta alguns desafios. O custo de aquisição e manutenção é mais elevado, exigindo investimentos em centros de usinagem compatíveis e práticas rigorosas de limpeza e lubrificação para garantir a performance esperada. Além disso, a compatibilidade com máquinas antigas ou de menor porte é limitada, o que pode dificultar a sua adoção em empresas com infraestrutura tradicional.
A empresa Haimer, referência global em soluções de fixação e balanceamento dinâmico, oferece ampla gama de porta-ferramentas HSK nas versões A, E e F, com controle rigoroso de qualidade, garantindo precisão micrométrica e balanceamento para rotações extremas. Confira o portfólio completo de cones porta-ferramenta da Haimer.
Conclusão: Qual cone escolher?
A escolha do cone porta-ferramenta em um centro de usinagem deve ser feita com base nas exigências específicas de cada processo produtivo, levando em conta fatores como velocidade de rotação, rigidez, precisão dimensional, tipo de material a ser usinado, nível de automação e custo de implementação.
Sistemas como o BT e o CAT oferecem robustez e ampla compatibilidade, sendo ideais para operações de usinagem mais simples e centros de usinagem mais antigos. O cone SK, comum em máquinas europeias, também apresenta boa rigidez e confiabilidade. Já o HSK se destaca em aplicações de alta rotação e precisão, especialmente em ambientes automatizados que exigem máxima estabilidade térmica e mínima vibração.
Não existe um sistema universalmente melhor, mas sim o mais adequado para cada situação. A decisão acertada garante maior vida útil das ferramentas, melhor acabamento das peças, redução de paradas e aumento da produtividade. Conhecer as características e particularidades de cada tipo de interface é fundamental para obter o melhor desempenho possível na usinagem.
A equipe da Róiz Máquinas, em parceria com a engenharia de aplicações de suas representadas de renome mundial, está preparada para ajudar os clientes a encontrarem a melhor solução para sua usinagem. Caso ainda tenha alguma dúvida clique aqui e fale agora com nossos consultores para encontrar a melhor solução para o seu processo de usinagem.